KACO needed a way to accurately place seal rings in and out of a sliding wax application system. The waxing process is the last step before the seals are inspected and shipped. Photo courtesy Zimmer Group
Radial shaft seals are used to seal rotating axles and shafts. They keep oil or transmission fluid in, and they keep dust and other contaminants out. They can be found in myriad applications, including cars, trucks, gearboxes, pumps, agricultural and construction machinery, and wind turbines. O Rings

A radial shaft seal consists of an elastomer bonded to a metal stamping. Two lips are typically molded into the elastomer. The primary lip faces inward to seal in the oil; a secondary lip faces outward to keep contaminants out. A garter spring surrounds the primary lip to supplement the radial force supplied by the elastomer.
The seal is typically installed in the bore as a press fit. The main lip and the dust lip engage the rotating shaft. The main considerations for designing and specifying a seal are temperature, speed, fluid and pressure.
Based in Kirchardt, Germany, KACO GmbH and Co. is a leading manufacturer of dynamic and static shaft seals, pressure compensation elements, encoders, shaft grounding rings, and other products for the automotive industry. The company got its start in 1914 making gaskets for car engines. Today, KACO employs some 2,000 people at six production facilities in Germany, Austria, Hungary, China and the US.
As engineers in Kirchardt were developing a new automated assembly line for radial shaft seals, they faced a challenge. They needed a way to accurately place seal rings in and out of a sliding wax application system. The waxing process is the last step before the seals are visually inspected and shipped to the customer. The wax acts as a lubricant, ensuring smooth installation.
To get the right gripper for the job, KACO turned to automation component specialist Zimmer Group. There were several key requirements for the application. First, because the gripper must handle seals in a variety of sizes, the stroke length had to be adjustable. That ruled out pneumatic grippers.
In addition, the application required internal gripping, since the rubber coating of the parts must not be damaged. Grippers offer two holding options: external and internal. Which to choose depends on the geometry of the part, the process to be performed, the orientation of the parts, and the physical space available. External gripping is the most common way to hold parts. The closing force of the gripper is used to hold the part. Internal gripping is used when the part geometry will allow and when the process to be performed needs access to the outside surface of the part. The opening force of the gripper is used to hold the part.
The application required internal gripping, since the rubber coating of the parts must not be damaged. Photo courtesy Zimmer Group
The GEH6040IL-03-B electric gripper turned out to be the best option for these requirements. Its IO-Link technology enables precise force adjustment and programmable control of jaw position and speed thanks to the servo drive. Up to 32 settings can be stored in the gripper, which facilitates adaptation to new workpiece sizes and saves time during production changeover.
The gripper has a maximum stroke length of 40 millimeters per jaw, and it provides a maximum gripping force of 1,000 newtons. Designed for durability, the gripper provides up to 5 million cycles without maintenance.
The gripper is equipped with a mechanical self-locking device. This ensures that the workpiece is held firmly in the gripper in the event of a power failure or emergency stop. In addition, the gripper has a mechanical emergency release, so it can be opened manually in the event of a system or power failure.
“The mechanical self-locking when the position is reached is a big plus,” says Klaus Tritt, technical consultant at the Zimmer Group, who supported KACO in this project. “It ensures that the workpiece is held securely in the event of an emergency stop or power failure.”
For collaborative robot applications, the gripper has an optional “safe torque off” function operated via a separate cable with two safe NC contacts. In an emergency, the power supply to the drive is interrupted directly in the gripper, meaning that it is immediately torque-free. It is possible to move again after closing the contacts without a restart time. This function corresponds to stop category 0 according to EN 60204-1.
With protection rating of IP54, the gripper is protected against the ingress of both splash water and dust. To further minimize wear in adverse environments, the gripper can also be equipped with a protector. A mechanical superstructure on the gripper protects against external influences, such as cooling lubricants containing water and oil. The gripper can operate in a class 4 clean room.
Based in Kirchardt, Germany, KACO is a leading manufacturer of dynamic and static shaft seals and other products for the automotive industry. Photo courtesy KACO GmbH and Co.
In KACO’s automated assembly system, two 6000 series grippers are connected in series to pick up parts from a conveyor, transfer them to the waxing station, and put them back on the conveyor for transport to the inspection station.
Integration of the grippers into KACO’s assembly line went smoothly. Close cooperation between Zimmer and KACO made it possible to develop a customized gripper that was perfectly tailored to the needs of the automotive supplier.
“The service and above all the technical advice from Klaus Tritt were always excellent. No matter what challenge arose during the integration of the grippers, Tritt was immediately at our side and was able to find a solution with us,” says Hubert Eckert, CAD designer and production optimizer at KACO.
Overall, the grippers have performed well. The application of sliding wax to the seal rings runs quickly and efficiently. Production costs have been reduced by half, mainly due to the saving of valuable time during setup for new seals.
For more information on grippers and other automation components, visit www.zimmer-group.com or visit Zimmer’s booth at The Assembly Show South, April 30-May 2, 2024, at the Music City Center in Nashville, TN.
You must have JavaScript enabled to enjoy a limited number of articles over the next 30 days.
On Demand Connecting shop floor tools to a manufacturing execution system is critical to error-proofing assembly processes, improving quality control, and lowering defect and scrap rates. Join Torrence Williams, Partnerships Manager for Pico MES, and Dan Smith, VP of Sales for Kolver Tools, as they discuss an easier path for manufacturers to start connecting their factory floor.
On Demand This topic is something that challenges each of us every day that we go to work. This talk is about change and why it works and why it fails. It is focused on manufacturing facilities, because that is where the author has spent most of his working life.
Copyright ©2024. All Rights Reserved BNP Media.
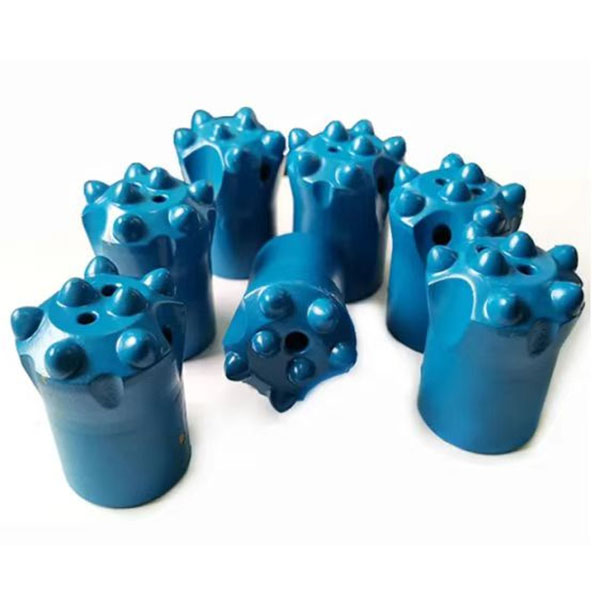
Flat Gasket Design, CMS, Hosting & Web Development :: ePublishing