The aerospace and defense industry (A&D) continues to use more heat-resistant superalloys (HSRA) and exotic materials such as Inconel 718, Hastelloy, Haynes, Rene and Nimonic. These materials have desirable characteristics—high strength, corrosion resistance and thermal stability—that make them able to withstand extreme conditions like the heat of a jet engine, which can exceed 2,000° F (1,093° C).
HRSA materials are used to manufacture turbine disks, airfoils, combustion casings, blisks and many more jet engine parts. However, these same characteristics make them difficult to machine, with machinability ratings below 20%. As a result, better cutting tools are required. Incoloy825/2.4858

Because superalloys and exotic materials are generally very hard (40 HRC or more), achieving productive tool life and machining efficiency is challenging. Some materials tend to work-harden during the milling process, and higher cutting temperatures may occur due to material heat resistance, causing damage to the cutting tool and workpiece, reducing the quality of the surface finish as well as dimensional accuracy. Material toughness and ductility can also make it difficult to obtain clean, precise cuts.
To address this shift to challenging superalloys and exotic materials, end mills must work optimally with the machine tool and setup for better processing, longer tool life and improved part results. And with the A&D industry back in full swing, fast and timely part deliveries are key.
For aerospace manufacturers looking for a fast roughing and pre-finish milling solution, new ceramic end mills for the high-speed rough milling of these alloys provide long tool life and exceptionally productive machining.
It is important to note that the machine tool must be properly set up to accommodate ceramic end mills. A rigid, robust machine with high rpm needs to support the tool at 3,000 surface feet per minute (SFM) versus 120 SFM, which is typical of carbide tools. The optimal zone to run the tools is on machines with spindles that can generate at least 20,000 rpm and have an HSK connection.
In addition, this is a dry machining application. High-speed cutting is required with rigid tool holding and part clamping to generate the heat needed to soften materials without causing abrasion or other damage. Also, as feeds and speeds are significantly different than when using carbide end mills, and the overall milling strategy may differ, it is recommended to work closely with technical support from tooling suppliers.
When the machine and ceramic end mills are set up properly, the results speak for themselves. Although the tools have a higher price than traditional carbide types, they save significant costs via their speed and longevity. For example, it took 45 minutes for a customer to machine a feature on an aero-engine component when roughing with a six-flute solid carbide end mill. By switching to a Cera-Cut end mill from Emuge-Franken, the manufacturer was able to reduce the rough milling time on this feature to seven minutes.
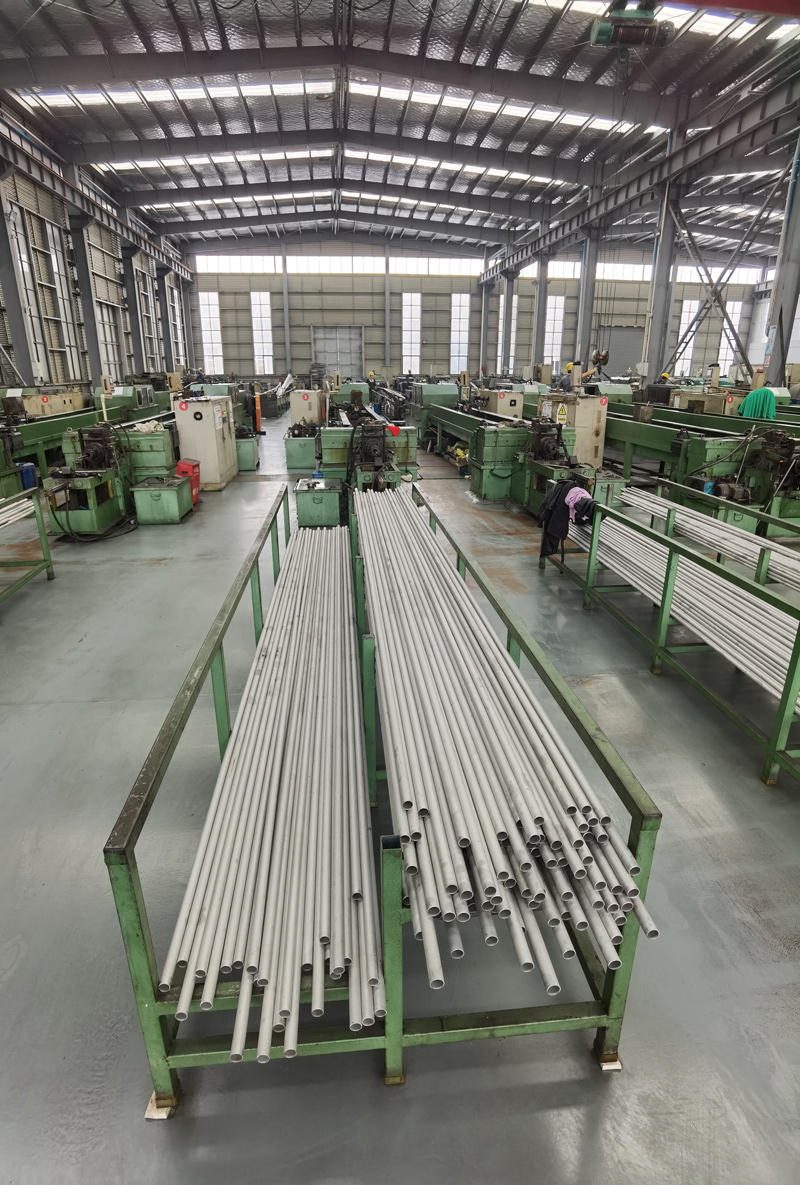
Inconel Metal In another example, a customer was making 33 passes using four one-piece solid ceramic tools to complete the rough milling on a feature in an aero-engine component. By comparison, the same rough milling process only required 10 passes and a single Cera-Cut end mill, which has a ceramic head brazed to a solid carbide shank. Conservatively estimated, this will save $100,000 annually compared to using the one-piece ceramic tool.