Single-step laser cutting and beveling eliminates the need for subsequent processes such as drilling and edge cleaning.
To prepare a material edge for welding, fabricators often make bevel cuts on the sheet metal. Beveled edges increase the weld surface area, which facilitates material penetration on thick parts and makes welds stronger and more resistant to stress. Laser Fiber Marking Machine
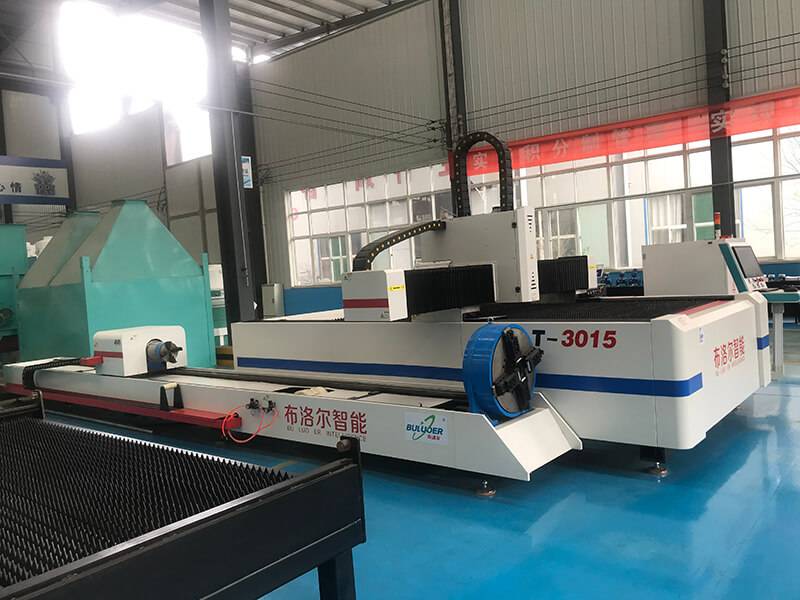
A precise, homogeneous bevel cut with the appropriate inclination angles is a primary factor in producing a weldment that meets the required code and tolerance requirements. If the bevel cut is not homogeneous throughout its entire length, automated welding might not be able to achieve the final required quality, and manual welding might be required to ensure the most control of the fill metal flow.
A constant goal for metal fabricators is to minimize costs. Integrating cutting and beveling operations into a single step can minimize costs by increasing efficiency and eliminating the need for subsequent processes such as drilling and edge cleaning.
Laser cutting machines equipped with 3D heads and featuring five interpolated axes can perform processes such as hole drilling, beveling, and marking in a single material input and output cycle, without the need for additional postprocessing operations. This type of laser performs interior bevels with precision through the length of cut and drills high-tolerance, straight and tapered small-diameter holes.
The 3D bevel head provides a rotation and tilt of up to 45 degrees, allowing it to cut a variety of bevel shapes, such as internal contours, variable bevels, and multiple bevel contours, including Y, X, or K.
The bevel head offers direct beveling of materials 1.37 to 1.57 in. thick, depending on the application and bevel angles, and provides a cut angle range of -45 to +45 degrees.
The X bevel, often used in shipbuilding, railway component manufacturing, and defense applications, is essential when the piece can be welded only from one side. Typically with angles from 20 to 45 degrees, the X bevel is most often used for welding sheets up to 1.47 in. thick.
In tests conducted on 0.5-in.-thick grade S275 steel plate with SG70 welding wire, laser cutting was used to produce a top bevel with a land with a 30-degree bevel angle and 0.5 in. high in the straight cut. When compared to other cutting processes, laser cutting produced a smaller heat-affected zone, which helped improve the final welding result.
For a 45-degree bevel, the maximum sheet thickness is 1.1 in. to obtain a total length of 1.6 in. on the bevel surface.
The process of straight and bevel cutting forms vertical lines. The surface roughness of the cut determines the final quality of the finish.
A 3D laser head with interpolated axes is designed to cut complex contours in thick materials with multiple bevel cuts.
The roughness not only affects the appearance of the edge but also the friction properties. In most cases, the roughness should be minimized, because the clearer the lines, the higher the quality of the cut.
A thorough understanding of the material behavior and interpolated movements for interior bevel cutting are crucial to ensure laser beveling achieves the end user’s expected results.
Optimizing fiber laser settings to achieve high-quality beveling does not significantly differ from the usual adjustments required for straight cuts.
The significant distinction between achieving optimal bevel cutting quality and straight cutting quality lies in the use of robust software that can support a variety of technologies and cutting tables.
For bevel cutting operations, the operator needs to be able to adjust the machine for specific tables that cater to exterior and perimeter cuts, but even more importantly, for tables that allow for precise interior cuts using interpolated motion.
The 3D head with five interpolated axes incorporates a gas supply system that facilitates the use of oxygen and nitrogen, a capacitive height measurement system, and an arm tilt of up to 45 degrees. These features help expand the machine’s beveling capabilities, especially in thick metal sheets.
This technology delivers all necessary part preparation in a single process, eliminates the need for manual edge preparation for welding, and allows the operator to control all processes involved in the final product.
See More by Antonio Calero
Read more from this issue
Find The Fabricator on Facebook
Find The Fabricator on Twitter
The Fabricator is North America's leading magazine for the metal forming and fabricating industry. The magazine delivers the news, technical articles, and case histories that enable fabricators to do their jobs more efficiently. The Fabricator has served the industry since 1970.
Easily access valuable industry resources now with full access to the digital edition of The Fabricator.
Easily access valuable industry resources now with full access to the digital edition of The Welder.
Easily access valuable industry resources now with full access to the digital edition of The Tube and Pipe Journal.
Easily access valuable industry resources now with full access to the digital edition of The Fabricator en Español.
Ryan Fielding of Ringbrothers joins hosts Dan Davis and Josh Welton on this episode of The Fabricator Podcast,...
© 2024 FMA Communications, Inc. All rights reserved.

Co2 Laser Marking Machine Not yet registered? Sign up