Drill bits are relatively inexpensive compared to other BHA components, but their performance has a significant impact on the cost of drilling a well. Although a PDC cutting element is relatively small, how it interacts with the formation has a large impact on rate of penetration and useful bit life. From an economic perspective, useful life determines the number of trips required to change out the bit. Conversely, ROP directly affects the drilling hours required to complete a given hole section.
With continuing advances in PCD cutter technology and improved bit body stability, PDC bits have practically replaced roller cone products. Their high ROP potential and unparalleled durability make PDC bits the tool of choice in high- and low-cost environments. This year, four companies have introduced new PDC technologies designed to positively impact performance and drive down cost/ft. Vertical Honing Machine
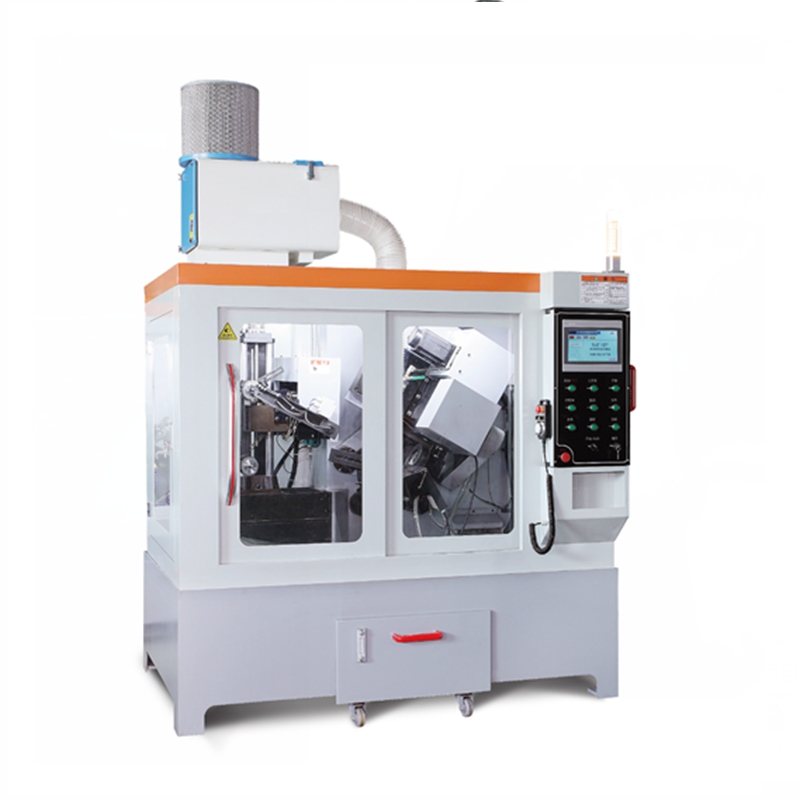
The increased application of PDC bits has accelerated over the past five years, due to the advent of shaped cutters. Although the implementation of shaped cutters in commercial PDC designs is relatively new, the idea dates to patents from the early 1980s. So, the question is, what is new?
First, cutters are now manufactured using HPHT in the synthesis processes that create stronger and tougher PDC material properties, and thicker PCD tables. Increased strength and diamond table thickness allow for more aggressive shapes. Second, increased computing power and improved software analysis enable engineers to optimize shape and cutter placement for specific applications. Lastly, as-pressed techniques, laser machining, grinding, or a combination of all three have improved manufacturing scalability. National Oilwell Varco (NOV) has continued a journey as a shaped-cutter pioneer by co-evolving cutter shapes, cutter grades, and drill bit configurations.
Rock failure efficiency focus. NOV initially focused on optimizing cutter shapes for cutter-rock failure efficiencies. These efficiencies needed to be significant while limiting other performance trade-offs like impact susceptibility or compromised thermal or abrasive wear resistance. The ION 3D cutter, which has a chisel or V shape, overcomes these challenges. It is mechanically stronger than a full round cutter in lab results, when compared on a full test in both medium and hard rock, performing so well in hard rock that it has led to more in-depth strength and toughness studies. New studies not only compare the shape strength but the different cutter grades with known strength differences. These lab results correlate directly with field results, Fig. 1 .
New technology pushed to limits. Operators inevitably pushed performance limitations by increasing parameters to meet ROP goals or increase interval lengths to reduce the number of trips. Ultimately, operators identified that thermal wear was limiting the life of 3D cutters. The first bit iterations contained 3D cutters in the cone area, with 3D shaped cutters placed in backup positions, as performance was proven. Eventually, 3D cutters were added to all primary positions. Cutters located in shoulder positions have increased linear velocity versus that of cutters nearer to the center of the bit. Increased velocity equates to increased temperature at the cutter tip. This is typically overcome using large depths of cut, which equates to increased ROP and reduced linear distance that the cutter tip travels, and equivalently reduced thermal input. In these cases, cutter placement optimization is needed.
A shaped-cutter optimization was performed in an 8½-in. Sprayberry lateral in the Midland basin. The objective was to improve ROP by reducing thermal wear in the shoulder of the bit. The base design was a six-bladed, 16-mm PDC bit using 100% ION 3D cutters on the primary cutting structure. Penetration rates and average intervals were limited by the abrasive formation, which was comprised of fine grain, silty sandstones with intermittent silty shale. Wear was initiated by the abrasive formation, developing large wear scars that generated more heat and created thermal spalls on the front of the cutters. A 37% more thermal and 54% more abrasion-resistant cutter grade was chosen. In conjunction, the drill bit was reconfigured with ION 3D cutters on alternating blades. The improved material characteristics and diamond coverage in the shoulder of the bit resulted in improved interval and ROP from 4,363 ft at 111.2 ft/hr to 8,743 ft at 138.8 ft/hr respectively. The dull was improved from 2-4-WT to 1-2-CT, with both bits drilling to TD at approximately 21,000 ft.
Improved cutter grade. In the Williston basin, ROP is the dominant performance metric; a technology advancement with as little as a 7% improvement will be adopted faster than in any other market globally. As such, the basin has become a testing ground for thermal-abrasion cutter grades. NOV, by iterating the material properties of the PCD table (better known as cutter grade), accounted for a conventional, full round cutter outperforming the ION 3D shape by staying sharper longer.
In an 8¾-in., six-blade, 16-mm upper vertical application, a new cutter iteration was paired against an alternating ION 3D shaped cutter configuration. The average interval was approximately 6,400 ft, with an average ROP of 206 ft/hr. The 100% full round configuration drilled 6,234 ft at 246 ft/hr, an increase of 29.1% in ROP and 25% decrease in IADC hours.
The transition to shaped cutters over the past several years has been slow. However, reluctant they may be, the results are clear and compounding the performance advantages of 3D shapes with improved cutter grades will continue to drive adoption.
New shape, new limits. NOV has introduced a second-generation shaped cutter series called the ION 4DX, based on the 4D shaped series previously trialed in the Williston basin. The 4DX is a nonplanar working surface that creates a plough effect in the shearing direction. Its third flank reduces contact surfaces and creates a fluid channel to break cutting ribbons into smaller pieces that are easier to evacuate from the drill bit face.
In an 8¾-in., six-blade, 16-mm, bottomhole vertical application in the Williston basin, the 4DX performed very well. The interval started at 8,100 ft and was typically between 1,800 to 2,200 ft. The design used a combination of ION 3D and ION 4DX shaped cutters to maximize crushing and shearing action on one drill bit, producing the rig’s fastest total vertical run and bottomhole vertical run over the previous 12-month period. The design achieved another fastest bottom vertical on another rig within the same period, in an adjacent county. On some initial runs, ROP increased 40%.
Material science innovation by Smith Bits, a Schlumberger company, has yielded a proprietary bit body material for improved drilling performance. The company’s Aegis* armor cladding (Fig. 2 ) significantly improves bit body design flexibility and erosion resistance, increasing ROP and bit durability for longer runs. Composed of a proprietary tungsten carbide material, Aegis cladding increases bit erosion resistance 400% and strength 40%, when compared to conventional matrix PDC bits.
The new armor cladding technology combines innovative materials science with an electron-beam additive manufacturing process. The new manufacturing approach allows the company to integrate proprietary material into customized, fit-for-basin bits, providing a differentiated technology to improve overall drilling performance.
In addition to improving erosion resistance, Aegis cladding enables bit designs with taller blades and optimal nozzle placement. This results in more efficient cuttings evacuation that improves ROP. The cladding has undergone extensive field testing across five shale basins in North America. The technology also has been field-tested in Europe, the Middle East and South America, in both onshore and offshore applications.
In Oklahoma’s Anadarko basin, two steel-bodied bits, with Aegis cladding, were deployed for an international company in eight wells for a total of eight bit runs. The use of the cladding increased ROP 36%, compared with direct offset runs using matrix PDC bits. The new bit technology saved the customer an estimated 179 hours of drilling time across the eight runs.
One of the biggest challenges facing the drilling industry is interfacial severity, or transitional drilling. This is broadly defined as layers of rock with different hardness that require the bit to drill through the transition, putting cutting forces on different parts of the profile. The imbalance of force concentration can induce vibration or even cause cutter overload, both of which lead to severe cutting structure damage.
Historically, bit companies would drill transition zones using heavy set bits with secondary features to control and limit the amount of force going through the cutting structure. They would also reduce drilling parameters to lessen force and “protect the bit”; a practice that has subsequently been proven to cause even more damage, because reduced weight or rotary speed can reduce the stability of the entire drilling system.
To solve the problem, an engineering team at Ulterra took a different approach. Bit designers developed an active cutting structure, called RipSaw, which regulates cutting forces, redirecting and absorbing force to increase stability, Fig. 3 . This is achieved without resorting to secondary features or high cutter densities, both of which can limit performance in other parts of the section. RipSaw’s patent-pending technology works like a shock absorber, allowing movement and high engagement, but preventing damaging shock and impact. Ulterra’s bit designers achieve this balance by using highly-engineered cutter positioning on different parts of the cutting structure. Depth of cut is regulated, but because all the cutters are fully engaged with the formation, work is optimized, and the bit continues to drill ahead efficiently.
West Texas case study. Ulterra first applied RipSaw in the extremely challenging 12¼-in. intermediate section in West Texas. The hole section is well-known as a definitive transitional application. The upper part of this section is relatively easy to drill, where the bit is pushed hard, and ROP is high. However, in the lower part of the section, the bit encounters hard and interbedded lithology, and the strategy switches to survival, trying to keep the bit on bottom as long as possible.
RipSaw bits have drilled almost 2 million ft of hole, on approximately 450 separate runs in this application, as part of an extensive testing program. Ulterra engineers ran a wide-ranging, macro-level field study of these bit runs and compared them to approximately 2,800 offsets. Examining this type of large data set eliminates the effect of outliers, both good and bad, while providing an objective review of performance and reliability over an extended period (six months).
Some of the most meaningful statistics to come from this study related to the first bit run on each section. This first run is crucial, since the deeper the first bit drills, the less work the next bit must perform to finish the section, increasing the chance of a more economical section cost. From the start, RipSaw technology increased the chance of scoring a shoe-to-TD run 28%, compared to other-type products.
A unique analysis method was used to create statistical risk profiles, which enable field engineers to model the probability of performance, based on the available data set. In this case, a risk profile was created for the first bit in every section, and how deep that bit drilled before it was pulled. Using this method, Ulterra determined that RipSaw bits had a 50% chance of hitting 7,000 ft on the first run out of the shoe. This compared favorably to other-type bits that had less than a 20% chance of hitting the same depth. RipSaw’s inter-quartile range was 2,000 ft deeper than other-type bits, and the median average run for RipSaw would have been an upper quartile run for any other product.
In other analysis, industry standard methodology was used to calculate bit run economics. Looking at all the runs combined, it was evident that RipSaw delivered exceptional value for the money, with a 39% improvement in cost/ft compared to other bit types. This was achieved by drilling further and deeper, and maintaining ROP compared to the average. Applying cost/ft for other-type bits to the total footage drilled by RipSaw theoretically saved operators a combined $74 million over this six-month period.
The first use of MARKSMAN directional PDC drill bits more than doubled the average rate achieved with offset hybrid bits (Fig. 4 ). The customized directional bits, developed by Varel Oil & Gas Drill Bits, use a highly adaptive design methodology that manages toolface control and side-cutting capability, based on specific application requirements.
In Canada, West Texas, and Oklahoma, MARKSMAN bits are delivering consistent yields to reliably drill build sections and reach objectives at significantly higher penetration rates. Directional bit design is generally a process of optimizing ROP and steerability to drill the curve section as quickly and consistently as possible. Considerations include cutting structure aggressiveness, steady torque, directional control, and dynamic stability, as well as ensuring the durability needed to reduce bit costs and increase time between trips.
In the build section of directional wellbores, PDC bit performance is complicated by factors, including the formation, wellbore geometry, the BHA design, and how the curve is drilled. The key to optimizing steerability and efficiency is effectively managing these dynamics to address the specifics of each drilling application
Design methodology. Designing MARKSMAN bits involves an understanding of how cutter size, blade profile, gauge length and other factors influence steerability and efficiency in a given wellbore geometry and geology. Gains in efficiency rely on how effectively this knowledge is translated into the bit design, and how well it complements the bottomhole assembly.
The design methodology may include variations in cutter orientation, cutter size, cutter density, and the bit profile. Greater steerability is achieved with a passive toolface that reduces the aggressiveness of the cone area toward the center of the bit. The toolface has a shallow cone angle and progressively less cutter aggressiveness from the shoulder to the center of the cone. Reactive torque is minimized, and steering response enhanced by a less-aggressive, higher-angle cutter back rake toward the center of the bit. The transition to a more aggressive cutter orientation on the shoulder improves side cutting and makes the bit easier to steer.
Key to the MARKSMAN concept is a fast, accurate response to specific applications. A suite of proprietary Varel software enables this bespoke process. Drilling scenarios, based on actual lithology, are simulated with PDC designer cutting structure design software. The simulation data support assessment of performance characteristics, such as lateral stability, durability and aggressiveness. DIG-IT software uses the data to run bit simulations in complex drilling scenarios, such as directional applications. The final data are imported into CAD software.
Case study. Initial drilling applications in Canada, West Texas, and Oklahoma illustrate the flexibility of this approach to directional PDC bit design: the Canadian bits are six-bladed with 11-mm cutters (611); in Oklahoma, they are typically 513 or 613 variations; and in Texas, 611, 513 and 613 variations are used, depending on formation and the BHA.
The first MARKSMAN application used a 6¼-in., 611 bit to more than double ROP in the build section, versus 11 offsets drilled with PDC/roller cone hybrid bits. In a second Canadian field for the same operator, the second bit run had similar performance.
In Sundance field, the bit run drilled the curve section of 1,640 ft at 79 ft/hr ROP, building from 16 to 90-degrees. The field-standard hybrid bits averaged 38 ft/hr over a 1,050 ft curve section. A second run in Kakwa field used the same bit design to build a 1,118-ft, 0 to 89° curve at 45.7 ft/hr. The offset average was 1,262 ft at 29.1 ft/hr. Both bits showed little wear.
In West Texas, there were back-to-back curve successes with a major operator in the Midland basin. The bits completed curves in 9.2 hr and 10.5 hr, respectively, with both bits continuing 1,000 ft into laterals in the Wolfcamp A formation. The bit/BHA combinations achieved yields ranging 13° to 18°/100 ft.
Oklahoma STACK and Merge applications also produced significant performance improvements. Designing the bits for the application resulted in configurations that varied from the Canadian bits. The two primary designs being used in Oklahoma are an 8¾-in., 513 and 613 configurations.
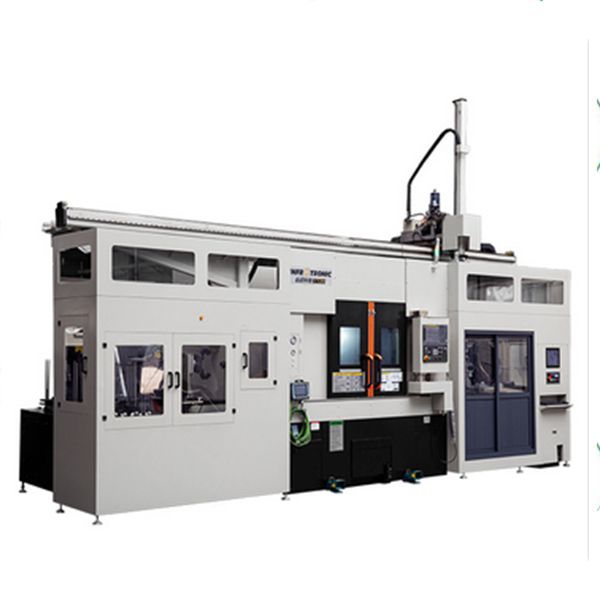
Gantry Drill The first Oklahoma run drilled a 687-ft build section from 15° to 90° in 15 hr for an overall ROP of 47 ft/hr. When merge runs of two identical bits were compared to other-type bit averages, the directional PDC design drilled 19% faster.